Antenna Control Unit
Mangata Networks is a startup founded in 2020, on a mission to create a new paradigm for satellite communications that improves broadband connectivity across the globe.
For my senior capstone project at Olin College, myself and four other students designed and prototyped a rugged, cost-effective antenna control unit (ACU) that tracks satellites via multiple modes of operation and allows remote control via a user interface. Over the course of the year, the team will researched satellite tracking methods, designed mechanical and electrical components, developed and tested versions of an integrated prototype ACU, created a graphical user interface, incorporated features for interfacing with 3rd-party products, and provided telemetry logging in an economical system.
Research:
Process:
At the beginning of the project, the team went through a research phase to learn more about program tracking, active tracking, calibration, and the electronics that would be needed for the ACU.
Alpha Prototype:
The mechanical design challenge for the first semester was to design and construct the alpha prototype of a pan tilt mechanism capable of housing the antenna dish, and meeting the technical specifications given by Mangata.
The system was designed out of 8020 extrusion and aluminum plates to make the prototyping process as simple as possible by reducing the amount of custom parts and increasing the speed of assembly. This was especially important due to this project taking place at athe height of the Covid-19 panemic.
The design was split into three major subsections: antenna mount, tilt head, and tripod base. Below are descriptions and CAD models for each major component of the alpha prototype.

Antenna Mount

Tilt Head

Pan Table

Tilt Head

Alpha Prototype CAD

Alpha Prototype
We learned a lot from the alpha prototype, and at the beginning of the next semester set out to apply what we learned to the design of a Beta Prototype.
Beta Prototype:
Using the lessons learned from the alpha prototype, we designed the Beta Prototype to be more aesthetically pleasing, and optimized for large scale manufacturing. The main difference was changing from 80/20 extrusion to folded sheet metal body. This drastically reduced the mass, complexity, and cost of the assembly. We also added a vacuum formed shell to protect the mechatronics from the elements.
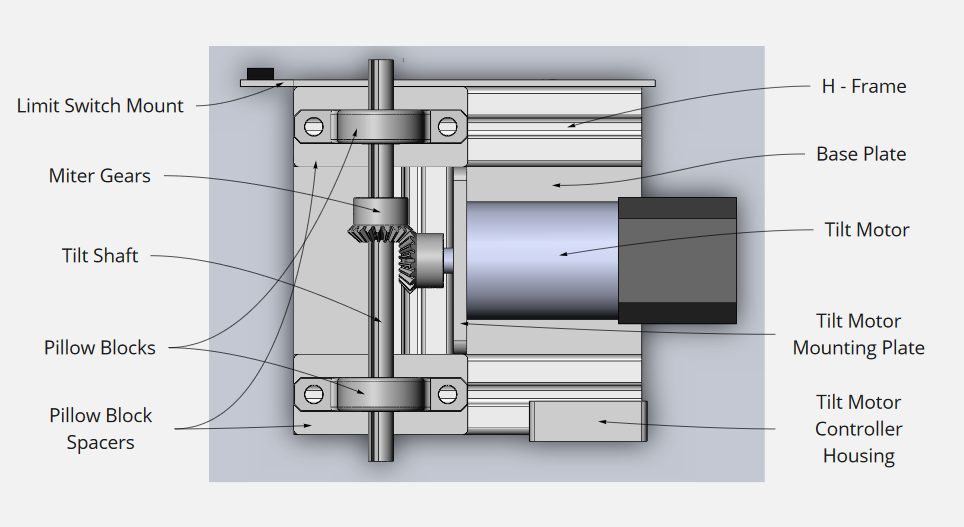